Streamlining Distribution
Streamlining distribution involves the planning and efficient use of supply chain resources and may involve working with intermediaries.
LEARNING OBJECTIVES
Describe the different elements that help streamline the logistics and distribution process
KEY TAKEAWAYS
Key Points
- The scope of the planning of logistics and distribution processes is not limited only to the planning of production, transportation, or distribution.
- In order to optimize the work of the logistics and distribution centers, one should define the criteria according to which the optimization shall be carried out.
- Distribution planning is based on the actual transport costs and requirements that represent single goods locations.
Key Terms
- supply chain: A system of organizations, people, technology, activities, information and resources involved in moving a product or service from supplier to customer.
- logistics: The process of planning, implementing, and controlling the efficient, effective flow and storage of goods, services, and related information from their point of origin to the point of consumption for the purpose of satisfying customer requirements.
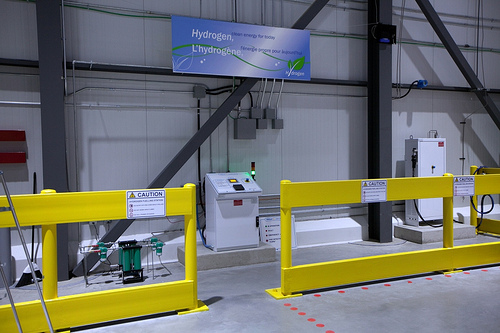
Distribution Center: Streamlining decisions go beyond the distribution center itself. It involves all of the elements in the logistics and distribution process.
Streamlining distribution involves the efficient use of all technologies included in the work of logistics and distribution centers. It should be mentioned that the scope of the planning of logistics and distribution processes is not limited only to the planning of production, transportation, or distribution. It covers the entire logistics and distribution process with all the elements.
No doubt the work of logistics and distribution centers greatly influences the entire logistic chain ( supply chain ), and therefore its optimal functioning is of great significance. In order to optimize the work of the logistics and distribution centers, one should define the criteria according to which the optimization shall be carried out:
- Sales planning
- Stock planning
- Supply chain planning
- Production planning
- Distribution planning
- Transport planning
- Delivery schedule.
Strategic and Long-term Planning
This element provides answers to the following questions:
- Which products do we want to manipulate?
- What market are the products intended for?
- In which manner can we avoid the conflict of the given objectives?
- In what way can we best use the assets and infrastructure in order to achieve maximal profit?
Creation of Supply Chain Network
This element optimizes the use of the necessary means in the current logistic network that includes suppliers, production locations, locations of distribution means, and end users.
Analyses and simulations allow testing of various combinations, i. e., the influence that opening a facility or moving the current infrastructure facilities will have on the total revenue and level of service. By performing various methods of logistic networks planning, the locations of new infrastructure facilities may be determined, which would meet the customers’ needs in an optimal way.
These methods are usually used for decision-making on whether larger quantities of stocks will be kept at one place or whether the transport costs of more frequent deliveries will be increased.
Demand Forecast and Planning
Demand forecast and planning with empirical knowledge (forecasts based on the demand within the previous period) use statistical data and mathematical functions. It may be said that demand forecast is a one-sided process, since forecasts are used as the basis for planning only the possible customers’ demand, rather than the quantity of goods that can be produced over the future period.
Sales planning
Sales planning can be defined as a process in which demand forecast is converted into a feasible operative plan that can be used by producers and salespersons. This process may include the planning of production and/or optimization of supply chains in order to determine the possibility of meeting the demand.
Stock planning
Stock planning allows the optimal level and location of finished products that meet the demand and the level of service of the end users. In principle, stock planning is used to calculate the optimal level of safety stocks at every location.
Supply Chain Planning
Supply chain planning compares the demand forecast with the actual demand in order to develop a “master plan” (schedule), based on the multi-level sources and critical materials. The developed master plan spans the points of production and the distribution destinations, with the goal of synchronizing and optimizing production, distribution, and transportation.
Production Planning
The term production planning means the development of a master plan for single factories (producers). The master plan is based on the availability of materials, factory capacity, demand, and other operation factors.
The production planning cycle represents a complex process that is, in the majority of considerations, represented as the start of the logistics and distribution processes. If these processes are considered from the other side (i. e., for the production of certain products, semi-products and raw materials are needed and are delivered to the factory), they then represent the final products for the factory and the end of one section of the logistics chain.
Distribution Planning
Distribution planning means the development of a feasible and viable plan of distributing end products from the producers (via logistics and distribution centers, warehouses, or crossdocking) to end users. Distribution planning is based on the actual transport costs and requirements that represent single goods locations.
Transport Planning
Transport planning uses current transport prices for the minimization of dispatch costs. In order to minimize the transport costs and maximize the usage of the fleet, transport planning means the optimization of both the external and the internal goods flow. One of the main transport planning functions is allowing and performing collective (bundled) transport of goods, and the inclusion of intermodal transport systems into the logistics and distribution processes.
Delivery Schedule
The function of delivery schedule is to create a feasible (realistic) plan that meets the time requirements for the delivery of the product by the producer. The producer determines the optimal methods and time of delivery, taking into consideration the receiving of orders, the production schedule, and the availability (planning) of transport.